
Vehicle Repair Network Management: Increase efficiency with multi-site connectivity & insight
Managing a multi-site bodyshop group, or large vehicle repair network, is an increasingly complex task. As vehicle technology advances, supply chains become more diverse, and demand for real-time data intensifies amongst work providers, networks are increasingly in need of more connected, centralised systems and processes.
Without real-time oversight of performance and exceptions across your network, it can be a challenge for operations leads to maintain efficiency, identify potential backlogs, and ensure cross-site consistency.
Here, we discuss why these challenges persist, and how repair networks can gain more control, consistency, and oversight across their multi-site operations – boosting performance and profitability.
The complexity of managing a multi-site bodyshop network
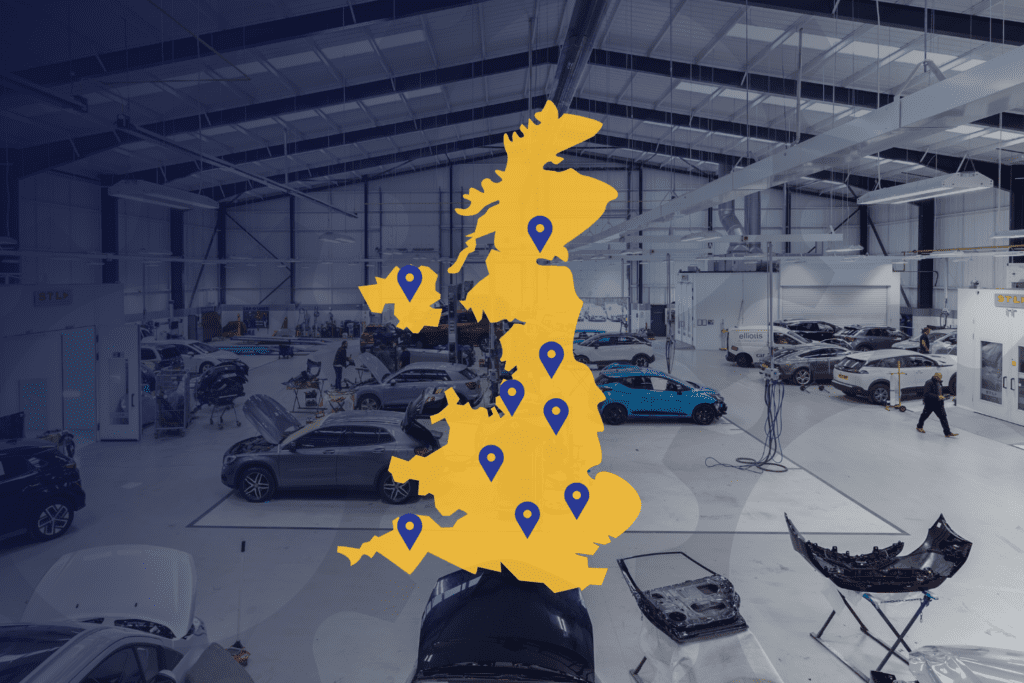
Maintaining an efficient, competitive repair network is weighted on far more than just individual site performance – it requires a connected approach to process efficiency, quality control, and strategic oversight.
As networks scale, these success factors can become increasingly challenging to maintain, particularly when sites rely on their own systems, communications, and reporting processes.
Here are some of the key challenges that come with managing multiple repair locations, and the impact they can have on top-level network performance:
1 – Maintaining consistency across multiple locations
In large bodyshop networks, each site may have its own way of working, making it difficult to standardise processes without restricting flexibility or innovation. However, differences in systems and workflows can lead to variations in service quality, efficiency, and compliance, making it harder to maintain consistency for work providers and the end customer.
2 – Lack of real-time visibility and reporting
Without real-time, centralised data, network stakeholders struggle to assess performance across multiple sites. Collecting and consolidating reports manually can be incredibly time-consuming, and prone to human error, leading to delays in decision-making. This makes it harder to forecast site workloads, track profitability, and ensure each bodyshop is operating at peak efficiency.
3 – High administrative burden
Multi-site operations require constant coordination between locations, which can result in an overwhelming amount of administrative work for operational leaders. Tracking job statuses, parts procurement, compliance, and performance benchmarks across multiple systems can slow teams down, and take their focus away from customer outcomes and operational efficiency.
4 – Managing cost control and efficiency
With the tight margins of many modern repair businesses, network managers need complete visibility over costs, cycle times, and resource allocation. However, without an integrated system, it becomes difficult to identify where inefficiencies are coming from – whether in parts procurement, technician productivity, or administrative processes.
5 – Meeting work provider and insurer expectations
Repair work providers like insurers and fleet operators increasingly require accurate, real-time performance data from their networks, to help them identify trends, mitigate risk, and develop more predictive models. If network partners are unable to provide detailed, structured reporting on repair cycle times, productivity, and compliance, they risk losing work provider confidence and falling behind more technologically adept competitors.
These challenges, and their time-consuming nature, mean that many networks find themselves reacting to exceptions and issues rather than proactively preventing their occurrence. Instead of focusing on continuous improvement and strategic optimisation, operations teams are often consumed by manual reporting, chasing updates across sites, and firefighting daily inefficiencies.
How can networks overcome these challenges?
To remain efficient and competitive, repair networks need a modern, integrated solution that provides clear oversight, automation, and efficiency at scale. By centralising operations and standardising processes, networks can ensure consistency across all sites while maintaining flexibility where it matters.
Replacing fragmented systems with a modern, central platform can enable seamless data connectivity, improved reporting, and greater control over performance, costs, and compliance.
This helps to ensure your network is not just managing challenges, but actively driving efficiency and growth.
Introducing…
Onyx BMS: Achieve network-wide efficiency, insight, and consistency
Onyx BMS is designed with multi-site vehicle repair networks front of mind, providing a scalable, cloud-based system that connects every location in one seamless, user-friendly platform – for complete oversight.
Centralised multi-site management
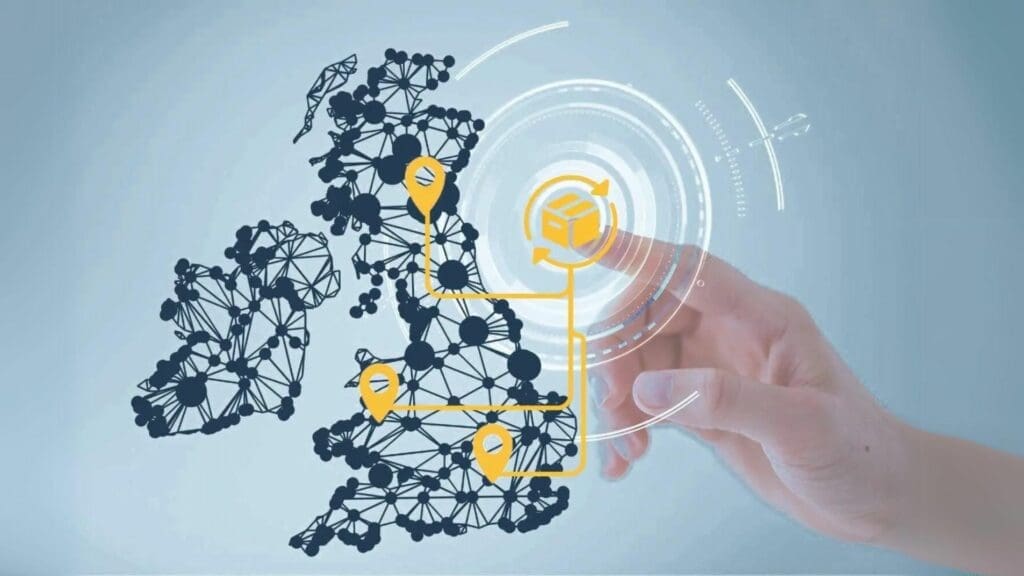
Onyx BMS gives network managers the ability to switch between sites at the click of a button, or select multiple locations at once, across every screen, report, and tool. With a single system for job tracking, task workflows, and data insights, operations teams can monitor performance, ensure consistency, and deliver compliance across the entire network from one place.
Real-time data insights and reporting
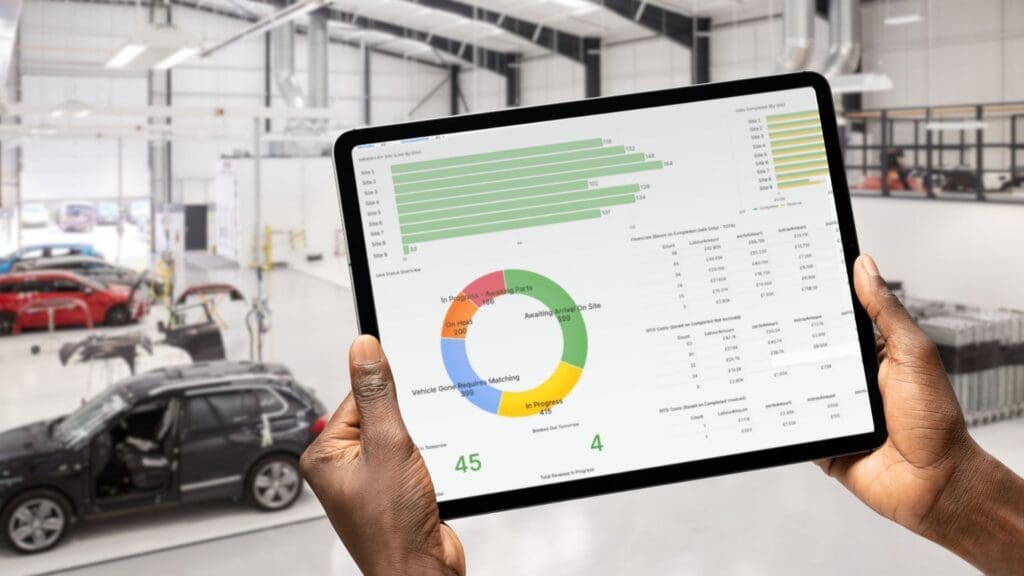
With Onyx’s live data dashboards, managers can track site-by-site performance, cycle times, financials, and operational KPIs. Data is updated in real time, so there is no need for manual reporting or time-consuming data consolidation.
Automated cross-site workflows
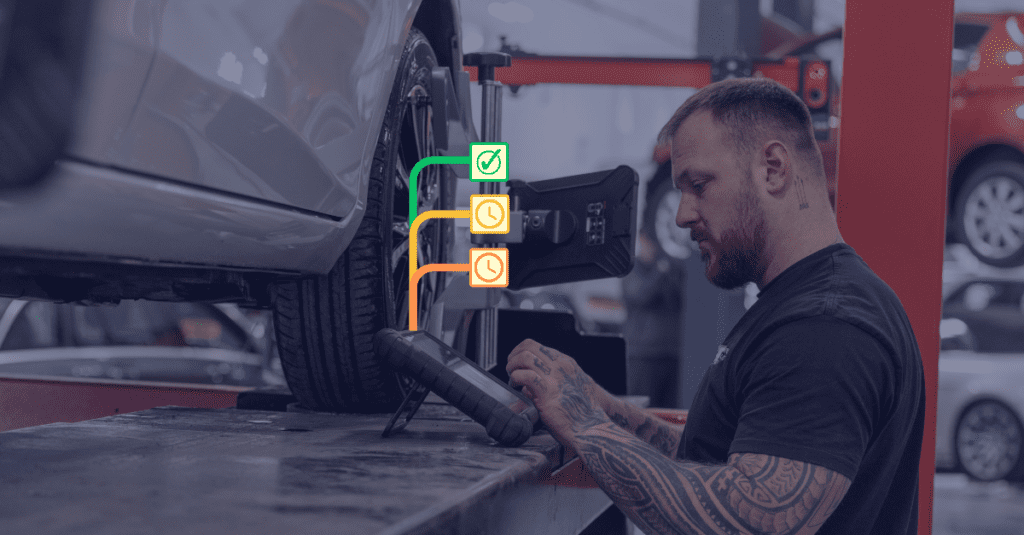
Onyx BMS streamlines job allocation, approvals, and task prioritisation across all sites, reducing the admin burden on teams. By automating key processes like repair estimates and orders, the system ensures tasks are completed faster, with fewer delays and less reliance on manual coordination.
Seamless communication across locations
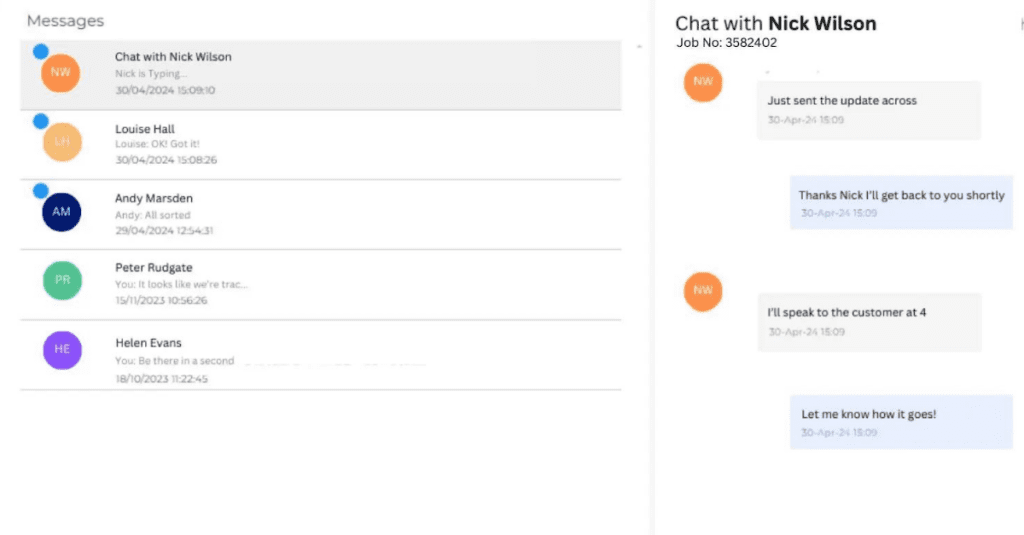
Onyx’s built-in instant messaging system allows network managers to communicate directly with site teams, and even individual techs, ensuring faster responses to operational exceptions, and real-time collaboration between locations.
Integrated cost control and forecasting
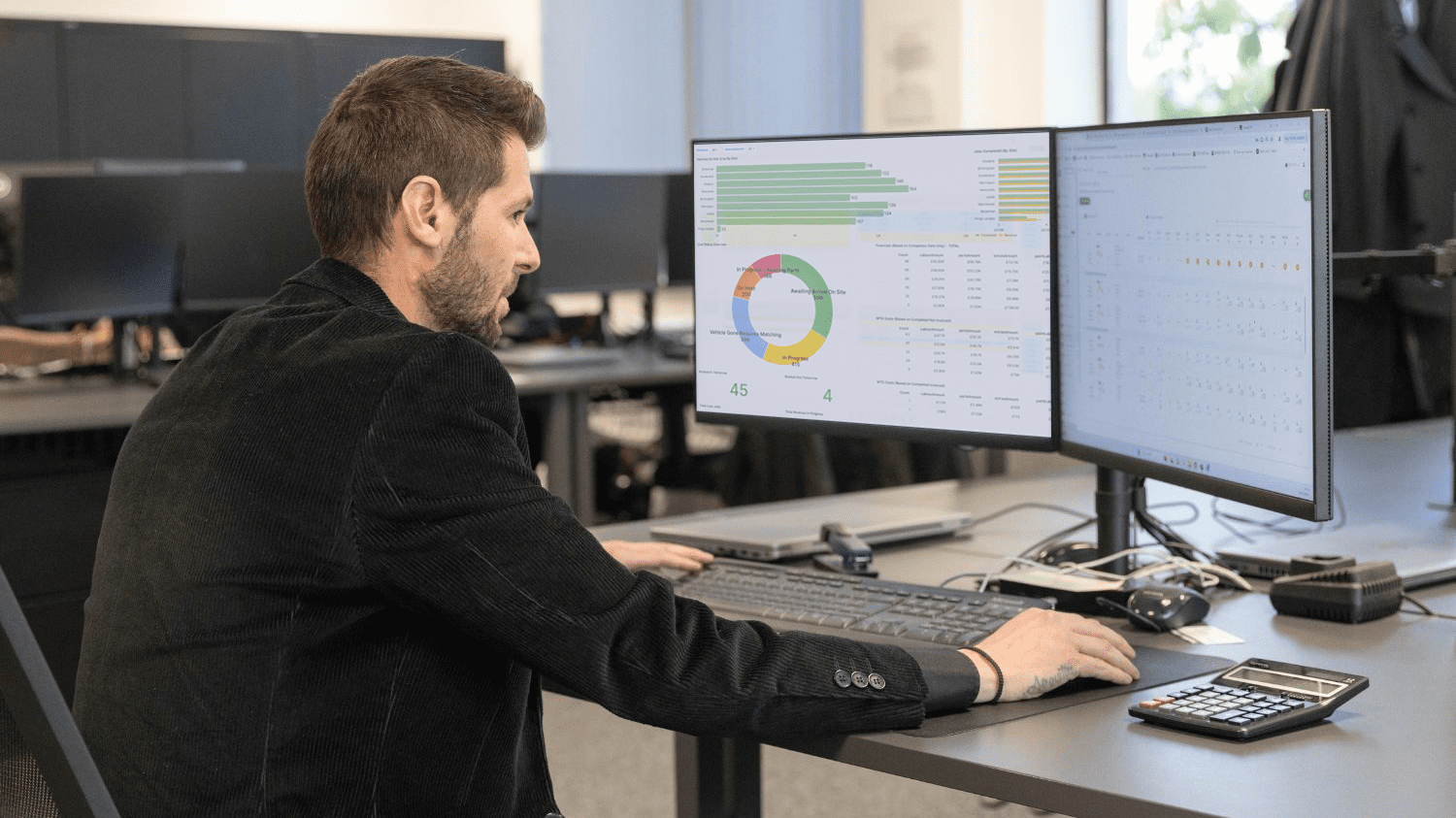
With real-time financial tracking, Onyx BMS helps networks identify where profitability is being lost, and where efficiencies can be gained. Managers can compare performance across different locations, track network-wide operational costs, and optimise staffing, investment, and resource allocation more strategically.
Work provider and insurer-ready reporting
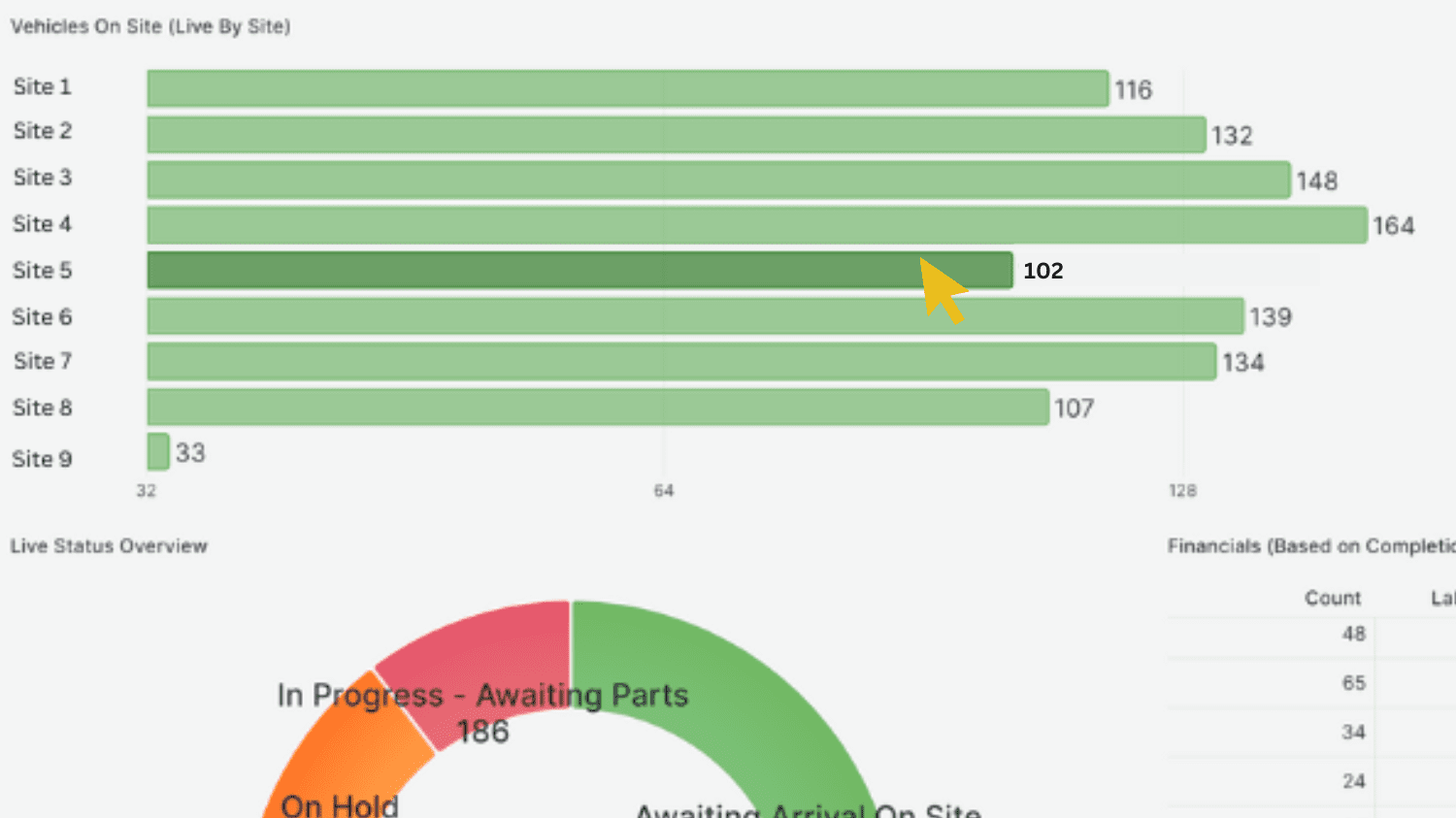
Onyx BMS makes providing structured, accurate data to insurers and fleet customers simple. With automated reporting, and simple data sharing, managers can ensure that their network is delivering the performance and technical insights that work providers find increasingly crucial, directly helping them drive more predictive operational models.
In Summary
For large-scale repair operations, efficiency, data visibility, and automation are essential for staying competitive. Onyx BMS provides a single, scalable platform that connects every site, standardises workflows, and eliminates inefficiencies—giving operations directors and network managers the control and insight they need to drive performance.
Find out how Onyx BMS can help your repair network work smarter, and drive performance, profitability, and insight:
Popular Posts
-
Vehicle Repair Network Management: Increase efficiency with multi-site connectivity & insight
Managing a multi-site bodyshop group, or large vehicle repair network, is an increasingly complex task. As vehicle technology advances, supply chains become more diverse, and demand for real-time data intensifies amongst work providers, networks are increasingly in need of more connected, centralised systems and processes. Without real-time oversight of performance and exceptions across your network,…
-
Rethinking Bodyshop Management Systems: A Strategic Shift for Repairers
For auto body repairers, Bodyshop Management Systems (BMS) have traditionally served one distinct purpose: to enable them to receive job allocations through platforms like CAPS. While this is undoubtedly a critical use case of any solid BMS, and a vital part of running a successful bodyshop, it’s not the full scope of what a truly…
-
How to Centralise Parts Procurement in your Bodyshop
Your average auto bodyshop goes through a lot of parts – that’s a given! They typically utilise a range of suppliers to secure the best price and turnaround across different components, vehicle manufacturers, and parts channels. But for many bodyshops, this process can be fairly disjointed; they’re often required to order directly from different suppliers,…
Leave a Reply